A Guide to Selecting the Right Molding Solutions for Your Business
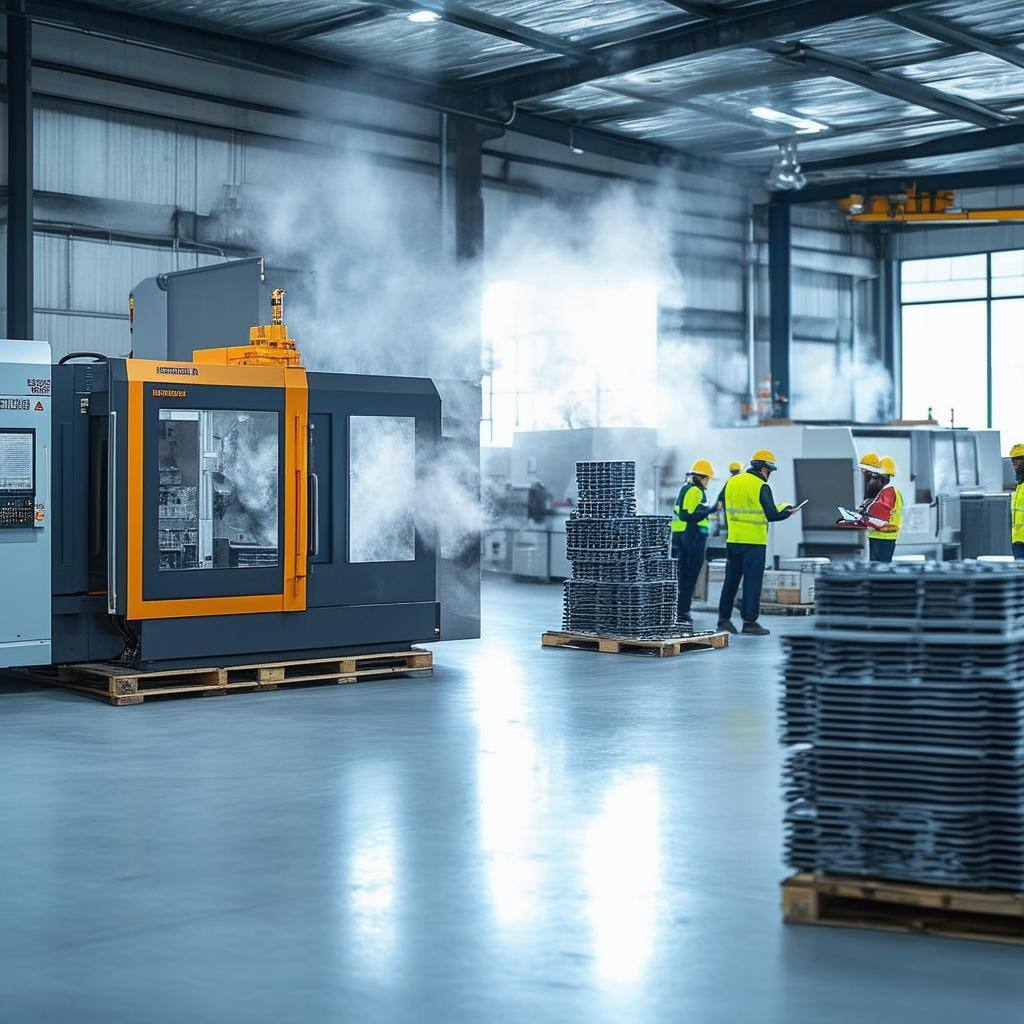
Molding plays an integral role in manufacturing, serving as a foundation for many products we encounter daily. Selecting the appropriate molding solution can be a daunting task due to the variety of materials and processes available. Businesses that make informed decisions in this area often find themselves better positioned for long-term success. This guide offers insights to help you choose molding solutions that align with your specific needs and objectives.
Understanding Your Molding Needs
Before diving into the various molding options, it’s essential to assess your business's specific requirements. Different products necessitate different molding processes, depending on factors such as durability, complexity, and volume. Products may need simple shapes or intricate designs, each affecting the choice of molding material and process. For instance, while larger volumes might lead you to opt for a more automated process, varying product designs may prompt considerations of different materials. Understanding these nuances will ensure you select a solution that meets both your quality standards and production goals.
Types of Molding Processes
Several molding processes exist, each with unique advantages and specific applications. Familiarizing yourself with these can guide your decision-making. Injection molding is a widely used method that involves injecting heated plastic into a mold. Due to its efficiency in producing high-quality parts at scale, many businesses opt for this method. Understanding advanced injection capabilities can further expand your production possibilities, which you can explore at www.technh.com/capabilities/plastic-injection-molding and manage all necessities. On the other hand, blow molding is ideal for hollow objects, this process uses air pressure to create containers. It's particularly popular for making bottles. Compression molding requires placing material into a heated mold where it is compressed, making it suitable for creating rubber or thermoset products. Understanding the pros and cons of each method allows businesses to match their product requirements with the ideal molding process.
Selecting the Material
The choice of material is as critical as the molding process itself. Various plastics, metals, and rubbers can be used, and selecting the right one influences product durability and functionality. For example, thermoplastics like polyethylene and polypropylene are excellent for injection molding due to their versatility and resistance to stress. On the other hand, elastomers like silicone offer superior flexibility, making them ideal for sealing applications. Assess the physical and chemical properties, budget constraints, and performance needs to determine the best fit for your project.
Cost Considerations
Cost is often a deciding factor when selecting molding solutions. Both initial tooling costs and long-term production expenses should be evaluated. High-quality molds may require a more significant up-front investment but can significantly reduce unit costs over time due to the efficiency of the production process. Additionally, consider ongoing maintenance costs for molds and machinery. It’s prudent to invest in high-quality solutions upfront to mitigate risks of defects and rework costs down the line, which can quickly add up and diminish profit margins.
Working with Professional Manufacturers
Partnering with established molding manufacturers can provide invaluable support in navigating the selection process. Experienced manufacturers offer insights into the latest technologies and materials, ensuring you make informed decisions. Furthermore, they assist in streamlining production and optimizing cost management. Collaborating closely allows for sharing ideas and troubleshooting challenges, resulting in a more effective production strategy. Take the time to research potential partners, reviews, and case studies to find a manufacturer who aligns with your business goals.
Evaluating Quality Assurance Processes
Quality assurance (QA) is essential in molding processes due to the potential for defects in molded parts. Developing a thorough QA plan can significantly mitigate the risks associated with product recalls or defects. Ensure that any production partner you choose has established QA processes in place to monitor quality at each production stage. Regular inspections, testing, and compliance with industry standards ensure that the final products will meet your specifications. The proactive approach to quality helps to build your brand's reputation and consumer trust.
Considering Environmental Regulations
Environmental impact is becoming increasingly significant in manufacturing, from compliance requirements to consumer preferences. Understanding the environmental regulations that apply to your materials and processes is vital for compliance and maintaining a good reputation. Eco-friendly materials and processes are on the rise, and integrating sustainable practices can enhance your brand. Innovation in biodegradable materials and recycling methods not only meets regulatory standards but also appeals to consumers' growing interest in sustainability.
All these factors combine to empower businesses when selecting the appropriate molding solutions tailored to their specific needs. Businesses have the opportunity to leverage these insights to inform their decisions, fulfilling both short-term project demands and long-term strategic goals.
Related Posts
Join the movement.
Your Entourage journey starts here. Join Australia's largest community of over 500,000 business owners and entrepreneurs, and receive instant access to exclusive content and updates delivered straight to your inbox.