Smart Manufacturing Moves That Cut Costs Without Cutting Corners
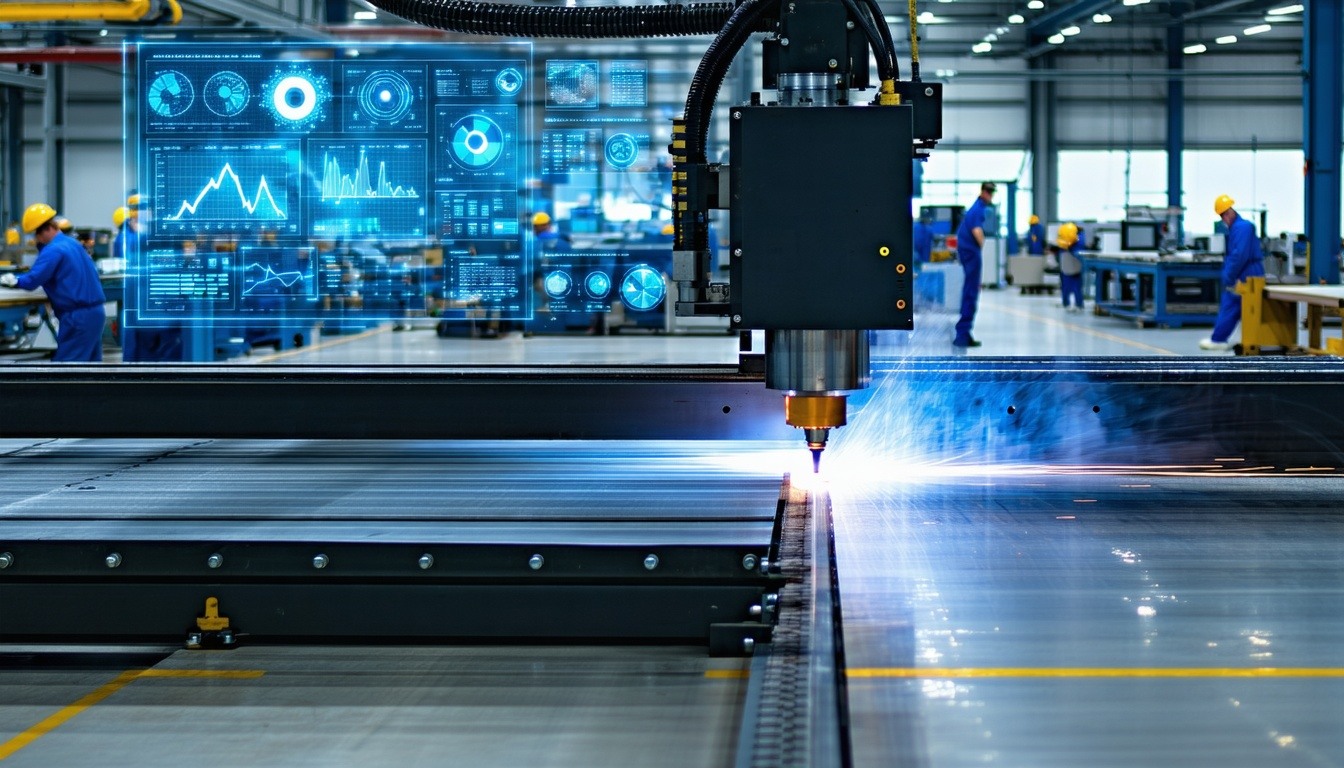
Cutting costs is always in the mind of manufacturing. But reducing expenses doesn’t mean letting go of quality. The smartest factories today are using smart strategies that lower overhead, improve results, and keep customers happy.
The goal is to work lean, not cheap. And with the right upgrades and approaches, manufacturers can get more done with fewer errors and less waste. In this article, we’ll break down simple, effective manufacturing moves that help you stay competitive—without cutting corners.
Let’s look at how you can save money and still deliver top-quality results every time.
1. Lean Into Lean Manufacturing
Lean manufacturing is all about doing more with less. It focuses on cutting out what you don’t need and improving what you already have.
Start by looking at your current workflow. Are there steps you can remove without affecting the final product? Are materials being wasted along the way?
Every small change counts. By removing unnecessary movement, overproduction, or waiting time, you make your process smoother. It reduces delays and increases productivity.
Lean manufacturing also improves team focus. When workers know each step matters, they’re more likely to stay sharp and engaged.
2. Upgrade Fabrication Tools for Precision
One of the most effective ways to cut costs is by reducing mistakes. And in fabrication, plasma cutting is one of the best tools to get there. Plasma cutting uses a high-speed jet of ionized gas to cut through metal quickly and cleanly. It’s widely used in manufacturing for its precision, speed, and versatility.
However, even plasma cutting needs the right setup to be efficient. That’s where choosing the right CNC plasma table becomes important. A CNC plasma table holds and moves the material precisely, allowing the cutter to follow an exact path. When paired with the right plasma system, it delivers smooth, consistent cuts with minimal waste.
A poorly chosen or outdated table can slow down the process, lead to errors, and waste materials. Therefore, you should read through guides ad talk to experts to choose the right one for your manufacturing needs. The right setup helps you save money, time, and materials—without sacrificing quality.
3. Automate with Purpose
Automation is no longer a luxury—it’s a smart investment. But it only works when used with intention.
Automate repetitive tasks that take up valuable time. This includes sorting, packaging, and quality control. These are areas where machines can work faster and more accurately than humans, reducing labor costs and mistakes.
It also frees up your team to focus on skilled tasks that require judgment and experience. When used properly, automation leads to fewer errors, better consistency, and higher overall efficiency.
Start small. You don’t have to automate your entire plant at once. Focus on high-impact areas and build from there.
4. Optimize Maintenance with Predictive Tools
Breakdowns can be expensive. When a machine goes down, it’s not just the repair bill you’re paying—it’s also the lost time, missed deadlines, and pressure on your team.
Predictive maintenance tools help prevent these issues. By using sensors and IoT devices, you can track how your machines are performing in real time. These tools alert you to problems before they cause a breakdown.
With early warnings, you can schedule maintenance during downtimes instead of rushing repairs during busy hours. This extends the life of your machines, keeps your operations smooth, and reduces emergency costs.
Over time, predictive maintenance saves money, builds consistency, and reduces stress across the team.
5. Improve Material Planning and Inventory Control
Materials are one of the biggest costs in manufacturing. Managing them well can save a surprising amount of money.
Start by using smart inventory software. These tools help you track what you have, what you need, and when you need it. They also help avoid overordering, which ties up cash in unused materials.
Better planning also reduces waste. You’re less likely to throw away materials that expire or become damaged from poor storage. You can also reduce the amount of extra space you need to store things, which lowers your facility costs.
Strong material planning leads to smoother operations and fewer surprises.
6. Train Employees in Tech and Efficiency
People are still the heart of manufacturing. The more skilled your team is, the better your entire operation runs.
Training your staff in new tech and systems helps you get the most out of every upgrade. Cross-training also makes your team more flexible, allowing them to step into different roles when needed.
An engaged and confident team makes fewer mistakes and feels more invested in doing quality work. It also helps you retain good employees—saving money on hiring and retraining.
Even small training sessions or weekly workshops can have a big impact on your bottom line over time.
Conclusion
You don’t need to sacrifice quality to save money. With smarter tools, better planning, and a skilled team, you can lower costs and still deliver great results. From automation to training employees, smart manufacturing is about working better, not cheaper. And that’s how you stay ahead.
Related Posts
Join the movement.
Your Entourage journey starts here. Join Australia's largest community of over 500,000 business owners and entrepreneurs, and receive instant access to exclusive content and updates delivered straight to your inbox.