Tips for Making Your Packaging Process More Efficient
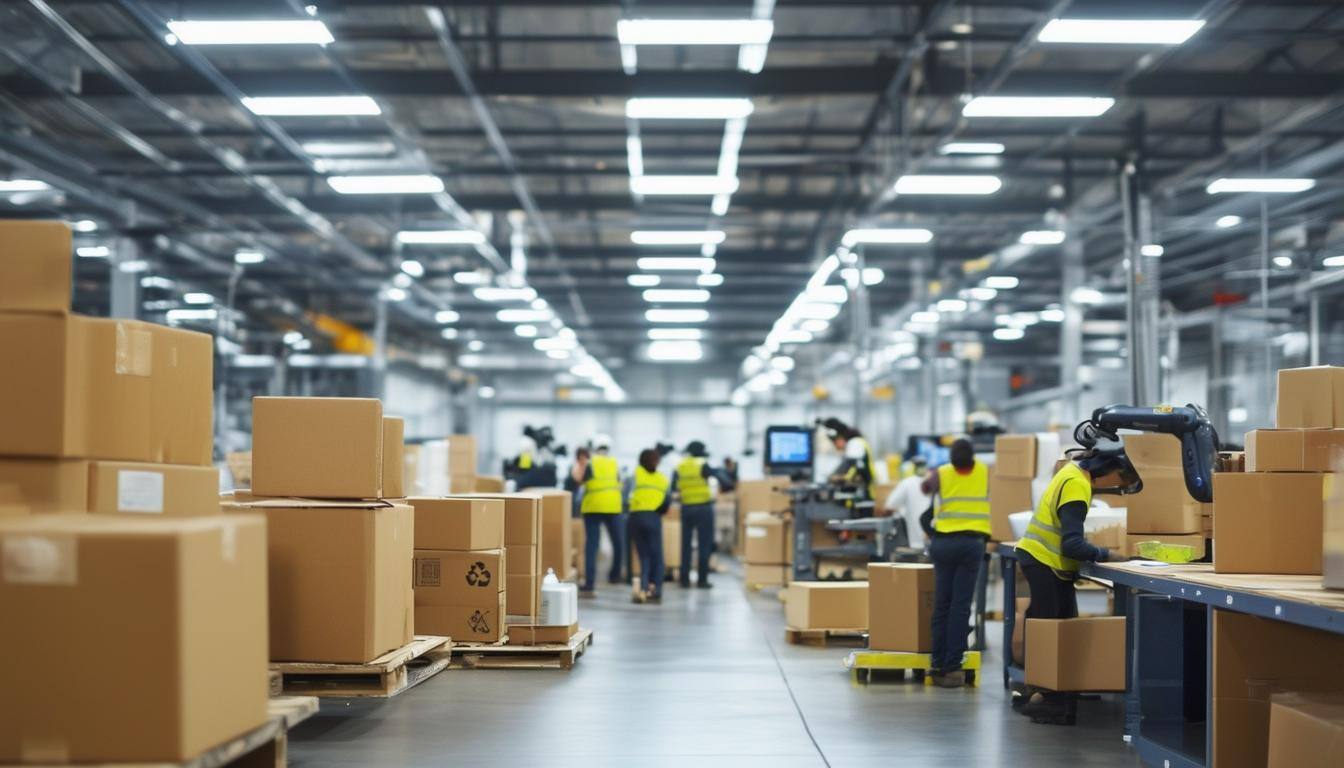
The efficiency of your packaging process can have a significant impact on the overall productivity and profitability of your business. As companies grow and evolve, it's essential to continuously refine packaging operations to minimize waste, enhance workflow, and improve the experience for both employees and customers. This article explores various strategies that can help streamline your packaging processes, ensuring that your business remains competitive in an ever-changing market.
Evaluate Your Current Packaging Process
Before making any significant changes, it’s necessary to conduct a thorough evaluation of your existing packaging process. Important factors to analyze include workflow efficiency, employee productivity, and material use. Gather feedback from your packaging team about challenges they encounter and areas that could benefit from improvements. Tracking metrics such as packaging time per order or error rates can provide quantitative data that highlights areas needing attention. By fully understanding your current operations, you can make informed decisions on where to implement changes. Efficient workflow is often a central theme in improving the packaging process. For instance, if employees face obstacles or unnecessary delays during packing, it’s crucial to identify those roadblocks. Perhaps certain materials are difficult to access, or specific tasks require excessive time. Such insights will guide you on how to modify your packing methods.
Optimize Your Package Station
An efficient package station is vital for speeding up the packaging process while ensuring quality. A well-organized package or packing station facilitates easy access to materials, tools, and equipment necessary for packing orders. Items should be arranged in a way that minimizes movement and allows employees to reach the materials they need quickly. Ensure that your packing bench includes a dedicated area for supplies, such as boxes, packing tape, labels, and protective materials. Organization not only boosts speed but reduces the risk of errors that can arise from a chaotic workspace. Furthermore, incorporating technology such as piece-picking robots, pick-to-light systems, and voice command picking can enhance efficiency significantly. These devices and features can automate some aspects of the packing process while providing valuable data on packing speed and materials used. Monitoring this data can help improve performance over time.
Utilize Training and Skill Development
Effective training programs are essential for ensuring that your employees are well-versed in packaging techniques and best practices. By investing in training, you enhance employee skills, leading to greater efficiency and fewer mistakes during the packaging process. Regular training sessions can help team members stay updated on new technologies or methods that could enhance their performance. Additionally, consider fostering an environment of continuous feedback. Encouraging employees to share their experiences and suggestions for improvement can lead to valuable insights that further streamline operations and processes. When your team feels empowered to contribute, they are more likely to excel in their roles.
Implement Technology
Integrating the right technology into your packaging process can lead to significant efficiency gains. Various tools and software options are available, ranging from inventory management systems to automated packing machines. These technologies help to speed up operations by reducing the manual effort required for repetitive tasks. For instance, automated machines can quickly seal boxes and apply labels, allowing employees to focus on more intricate aspects of the packing process. Monitoring inventory through digitally integrated systems also enables you to keep track of materials and supplies seamlessly. You can establish alerts when stock runs low, avoiding work stoppages due to insufficient packing materials. As a result, implementing advanced technology can significantly streamline your operations while minimizing the chance for error.
Rotate Responsibilities
Another strategy for improving efficiency is to rotate employees' responsibilities within the packaging process. Allowing team members to experience different roles not only fosters a more engaged workforce but also leads to increased versatility and problem-solving skills. By understanding various tasks in the packaging process, employees can identify bottlenecks and offer valuable improvements based on their firsthand experiences. Regularly changing roles encourages collaboration within teams, leading to a more cohesive work environment. This shared understanding can pave the way for innovative solutions to efficiency challenges, as team members work together to optimize the packaging process each day.
Consolidate Packaging Materials
Explore the possibility of consolidating packaging materials to streamline inventory management. Instead of using various types of boxes, tape, and fillers for different products, consider standardizing materials where possible. This not only simplifies the packing process but also reduces the complexity of inventory management. Standardizing packaging can lead to cost savings, as buying in bulk frequently results in lower prices. Enjoying uniformity in packaging also allows for a quicker assembly line, as employees become accustomed to working with a smaller range of supplies. Equally important, a cohesive look can enhance branding and create a more professional appearance for your transactions.
Monitor Performance Metrics
To ensure continuous improvement, it’s crucial to monitor performance metrics regularly. Tracking key performance indicators (KPIs) related to your packaging process will enable you to identify successes and areas for improvement. Measures such as order-processing times, error rates in packing, and customer feedback on packaging quality can provide insights into how well your packaging operation is performing. Additionally, regularly reviewing these metrics allows you to adapt to shifts in demand or operational capacity. If an unexpected increase in orders occurs, for example, you can adjust staffing and resources accordingly to maintain efficiency. By continually analyzing performance data, you position your business for ongoing success.
Emphasize Sustainability
Focus on making your packaging process more sustainable, as consumers increasingly prioritize eco-friendly practices. Selecting sustainable materials and practices can lead to cost savings in the long run while enhancing your brand's reputation. For instance, using biodegradable materials or reducing packaging sizes not only decreases environmental impact but can also lower shipping costs due to reduced weight. Adopting sustainable practices requires examining every aspect of your packaging, from the materials used to the design process. Sustainable choices can resonate positively with customers, marking your company as a responsible and attractive option in the eyes of consumers.
Seek Customer Feedback
Receiving feedback from your customers about their experiences with your packaging can provide powerful insights into areas for improvement. Regular surveys or direct requests for feedback can help you understand how well your current packaging meets customer expectations. Utilize this information to make informed decisions about future packaging strategies, choices, and improvements. Customer feedback can also unveil issues you may not have noticed internally. Problems such as difficulty opening packages or damaged products during shipping can lead to negative perceptions of your business. Actively seeking feedback for improvements can contribute to a positive customer experience and strengthen your relationship with clients.
Review Regulations and Compliance
Particularly in heavily regulated industries such as food, pharmaceuticals, or electronics, keeping up with packaging regulations is non-negotiable. A thorough review of compliance requirements for the materials and methods you use is crucial. Non-compliance can lead to delays, fines, or even legal challenges, all of which have an impact on your operational efficiency. Regularly reviewing your compliance with industry standards not only keeps your operation functioning smoothly but also protects your business. As these regulations can change, being proactive about staying informed ensures that your packaging processes continue to meet legal requirements.
By implementing these strategies, businesses can enhance their packaging efficiency, which can lead to higher profitability and overall customer satisfaction. Whether through optimizing personnel roles, adopting new technology, or focusing on sustainability, every improvement helps create a more streamlined process. Efficient packaging goes beyond just getting a product ready for shipment; it reflects on the entire operation, impacting everything from labor costs to customer feedback. As your business grows and evolves, reevaluating these processes will keep you competitive while ensuring the best possible outcomes for your customers.
Related Posts
Join the movement.
Your Entourage journey starts here. Join Australia's largest community of over 500,000 business owners and entrepreneurs, and receive instant access to exclusive content and updates delivered straight to your inbox.